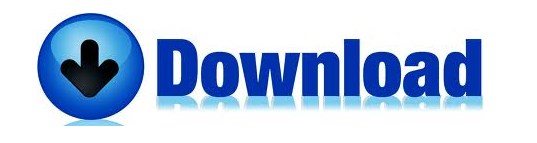
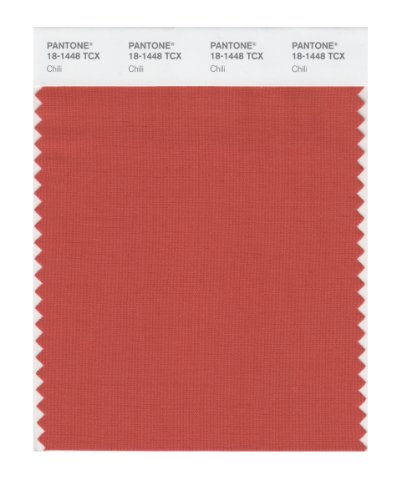
The digital cutter and computer will allow you to cut designs onto the HTV.Īfter the design is mirrored and then cut, use a weeding hook to remove the excess HTV from the sticky carrier paper so you are left with the design. To use HTV you need a digital cutter such as a Cricut Maker or Silhouette Cameo 3 machine and a computer with the cutting machines software.
#Vinyl master pro pantone colors how to
You can get lots of free or cheap designs if you don’t know how to create your own designs.Can be applied with a home iron, easy press or heat press.
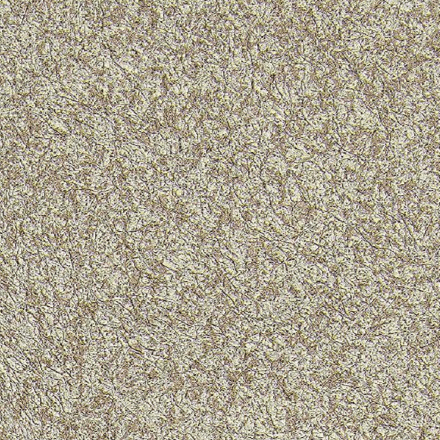

America Cut File Pros of Heat Transfer Vinyl Once you apply the HTV you peel the carrier paper off and are left with a finished product. Most HTV has a carrier paper which is the clear, polyester backing on the HTV often referred to as the ‘shiny side’. They also happen to be some of my favorite sites to order from.) (I shared the cheapest HTV sites in an older post I wrote. Heat transfer vinyl can be purchased from craft stores or online vinyl shops. Heat transfer vinyl is also referred to as HTV or iron on vinyl. Most HTVs say they can be applied with a home iron but you aren’t able to control pressure or temperature so I find a heat press works best. Different HTV brands and colors may require varying pressure, temperatures and press times (AKA not all of them are made the same). It is applied using a combination of heat, pressure and time. Heat transfer vinyl is a plastic based material that can be applied to shirts and other promotional products. Heat Transfer Vinyl What is Heat Transfer Vinyl? After searching the internet I found heat press transfers as an alternative. I had so many orders coming in I didn’t have time to cut and weed all the designs with heat transfer vinyl. I started using heat press transfers about six years ago when my Santa Sacks became wildly popular on ETSY. Lately I’ve shown how I use heat press transfers for large shirt orders I get on Instagram but I still use HTV the most. Today I am explaining the difference between Heat Press Transfers (also referred to as screenprint transfers) and Heat Transfer Vinyl. I may recieve a small commission, at no cost to you, if you make a purchase through a link.** Until you take that step, anything you try is going to require some sort of workaround, somewhere.**This post contains affiliate links to products I use and recommend. And since there's no way to make custom profiles in Rasterlink, unless you want to buy their module, which for the same money you could come damn close to real live robust RIP, then there's no way to get to where you need to be.īottom line, honestly, is if you're serious, first item on the agenda is a new RIP. However much they (your profiles) are off from how your printer actually prints, then your printed results will be off by that amount as well. However, sending the right L*a*b* value is only going to work exactly if your profiles describe how your printer actually prints in whatever condition you're using. However, what he's doing will work, as far as sending the same L*a*b* call to the printer as you would if you had an actual Pantone library. It's the alternate color that the guy in the video is replacing, although I don't think he exactly knows that.
#Vinyl master pro pantone colors license
Second problem is that - as has been pointed out, and again unlike Roland with Versaworks - Mimaki didn't pony up the license fees to Pantone, so either you're going to have to do some sort of workaround, like the little video fiddler showed, or your file is going to print using what's called the "alternate color" in the Postscript description (this is true in an. In Rasterlink, without the module, it's not possible to make profiles at all.
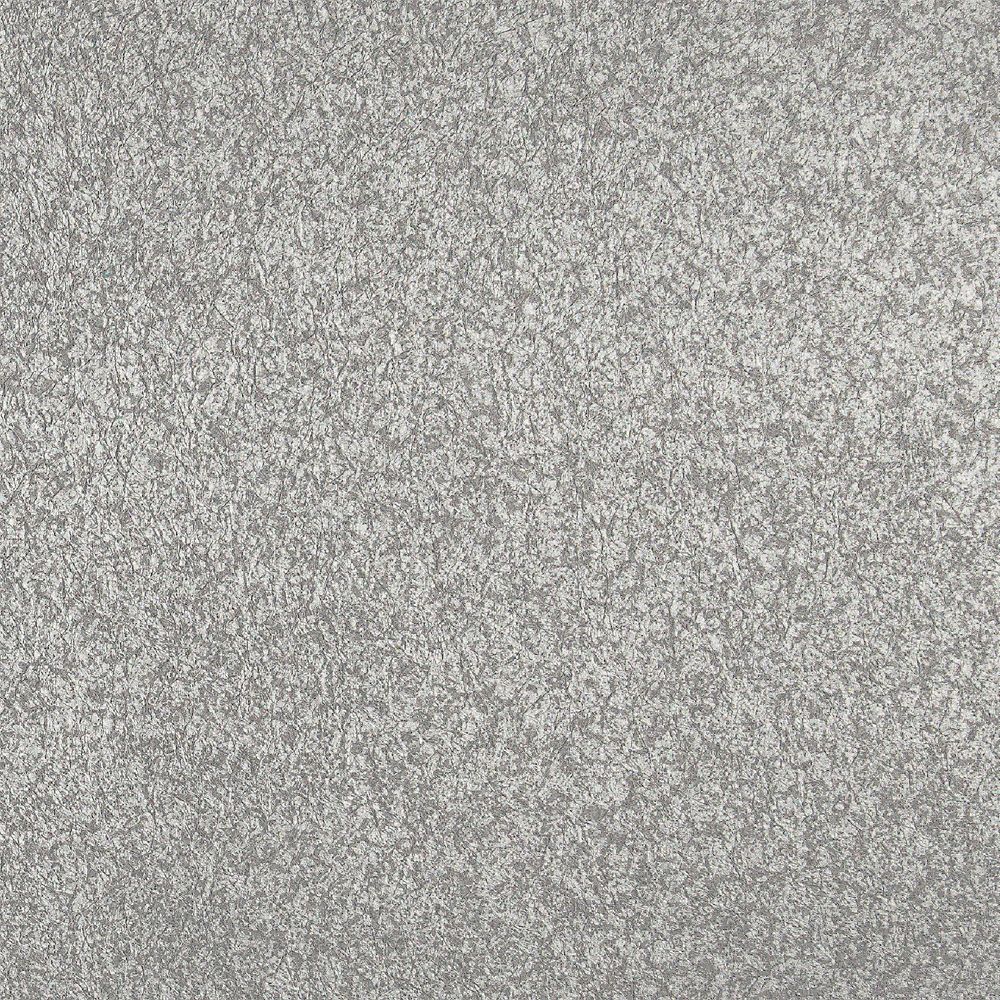
And note that this is different from Versaworks, which can be used to make machine states but needs a third party application to make ICC profiles. First is that unless you have the ridiculously overpriced profiling module, it's not possible to make profiles in Rasterlink at all. The problem is you've basically got two things working against you.
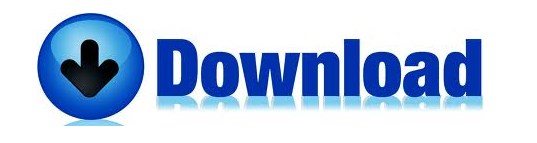